
The molds in the aluminum frames that were used to injection-mold the plastic blue butterfly were 3D printed on a Form 2 desktop stereolithography (SLA) 3D printer. Image courtesy of Formlabs Inc.
Latest News
September 5, 2017
Want to learn the true meaning of the expression, “frustrating endeavor”? Price out the cost to mill metal molds for injection-molding low volumes of small parts in production plastic that makes budgetary sense. These costs often cause you to nix good ideas or opt for third or fourth best concepts. Today's Check it Out presentation describes a study of an affordable way to create molds for short runs that you can deploy in-house for a faster, more nimble design process.
“Injection Molding from 3D Printed Molds” reports on a study that teamed a Formlabs Form 2 desktop stereolithography (SLA) 3D printer with a Galomb benchtop Model-B100 Injection Molder. The object was to determine if you could create a synergy between the two systems and make molds for small, functional parts for final products. The molds needed to withstand the temperature and pressure of the plastic injection-molding process as well as last for 10 to 100 parts.
The short of it is yes, it works. But what makes this paper intriguing is that you're walked through the project. The methodology, including post-processing 3D parts, is so well detailed that, later on, you should be able to follow the recipe to judge for yourself the potential of integrating this capability into your workflow.
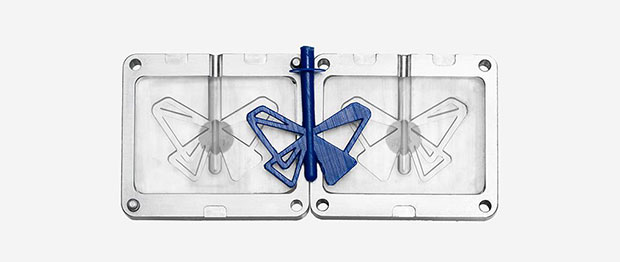
This white paper kicks off with a brief introduction defining the scope of the project and some of the attributes of the Form 2 SLA printer brought to the project, such as producing chemically bonded parts that are fully dense and isotropic.
Next come the granular details. Two mold designs were 3D printed in a clear resin. One mold had a single part; the other had four small parts. A third mold of a USB enclosure was made with a high-temperature resin.
The discussion covers the how, what and why of the test steps. Likely problems such as flash and too-visible part lines are addressed and corrections offered. The paper is frequently illustrated with photos, charts, tables and links to supplementary information like data sheets and third-party suppliers. At its end, the paper offers a set of design guidelines for early adopters.
“Injection Molding from 3D Printed Molds” is written with a moderate level of technical details, making it readily accessible to designers, moldmakers and engineering managers alike. It's a convincing and illuminating read. Hit today's Check it Out link to download your copy.
Thanks, Pal. – Lockwood
Anthony J. Lockwood
Editor at Large, DE
Subscribe to our FREE magazine,
FREE email newsletters or both!Latest News
About the Author

Anthony J. Lockwood is Digital Engineering’s founding editor. He is now retired. Contact him via de-editors@digitaleng.news.
Follow DE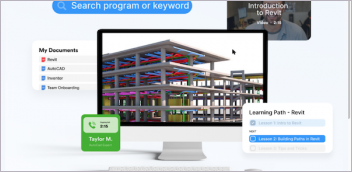
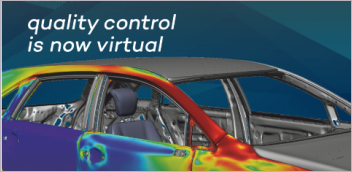
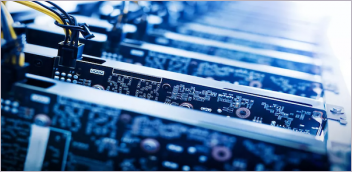
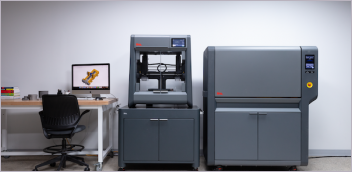