Simulation’s Missed Opportunity
Those of us in the simulation domain are well aware that the design insights revealed through simulation can dramatically speed product development, improve product quality, and lower the overall costs of products.
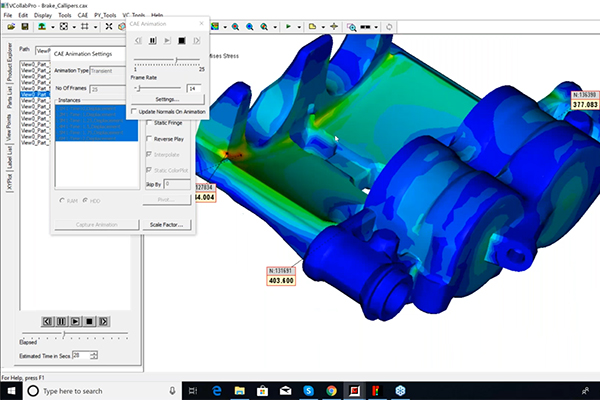
Latest News
March 4, 2020
Until now, however, technology and industry have focused on the front-end of CAE process automation; investment has targeted modeling, pre-processing, and solving simulations. The pre-processing phase, in particular, was a major pain point for analysts, who spent an enormous amount of time cleaning up CAD models, extracting neutral surfaces, and creating the right mesh, but these challenges are being addressed.
What’s been missing, however, is investment in post-processing and in capabilities for sharing and collaborating on simulation results and insights. I wonder if this is because simulation results were not previously on the critical path of the design decision process. Instead, test results played a crucial role in validating products and releasing them to production and manufacturing.
Today, however, simulations are on this critical path and the need to review and make design decisions based on simulation results has become a mandatory step in validating designs. So, what does this mean for simulation analysts, product designers, OEMs, and suppliers?
Let’s take a look.
Today, simulation analysts must use manual, time-intensive processes to create results that can be shared across the extended design team
- Post-processing must be done manually, critical hotspots can be overlooked.
- CAE reports for members of the extended design, manufacturing and supplier teams are typically created by simulation analysts, who must select, cut and paste 2D images from the original high-fidelity, 3D simulation results, into an easily shareable form like PowerPoint.
- The process of creating these reports is painful and time-consuming and must be repeated each time a design engineer, for example, requests a change to simulation parameters.
Design and release engineers, OEMs, and suppliers must make critical product decisions using less than complete information
- Critical product design and development decisions are made using low-fidelity, 2D information which has been reduced in quality to fit available reporting methods.
- Analysts must make educated guesses about which “snapshots” of data to reduce to 2D for sharing. They are not able to show users the original, high-fidelity 3D results.
- The time needed to create results reports – including multiple iterations – is long, which lengthens product timelines.
- And even if post-processing is automated, collaboration on design information is still less effective because current tools produce low-fidelity, 2D static images, which reduce context and omit key insights.
In short, the value created by simulation is reduced — unnecessarily. I say unnecessarily because,
There is a solution
For more than a decade we have been working to both improve and automate the content and ability to share simulation results.
VCollab delivers high-fidelity, 3D simulation insights. Automatically-generated, 3D views don’t need to be reduced in quality to 2D snapshots in order to be widely shared. Automatically generated comparisons of product behaviors and variants, the automatic identification of hotspots, and the ability to add context to simulation models using product performance information, all make it tremendously faster and easier for analysts to share insights. Insights that are actionable.
There are two important elements to our solution:
VCollab automates post-processing
For example, VCollab can automatically:
- Show the behavior of parts, or parts within assemblies, in 3D animated form.
- Identify hotspots within simulation results.
- Show behaviors of multiple designs, in a single 3D view.
- Show multiple stress loads in a single 3D view.
- Create these 3D easily-shareable views from virtually any CAD or CAE tool.
VCollab automatically creates these views; it also offers the authoring of automation templates that create complete reports, including all relevant product performance information.
With VCollab, the time and effort analysts must spend creating simulation reports can be measured in minutes rather than hours, while the completeness of information shared is substantially greater.
While it’s true that report creation can be automated without VCollab, it’s important to know that what is being automated is the creation of 2D, low-fidelity information. In other words, simulation result automation without VCollab produces lower-quality results reports faster – without meeting the needs of stakeholders.
VCollab enables simulation results & actionable simulation insights to be easily shared
VCollab extracts and combines information from multiple CAD and CAE sources in a compact, vendor-neutral format. It enriches simulation models and results with product performance information, creating high-fidelity actionable simulation insights for stakeholders.
VCollab simulation results:
- Can be panned, zoomed, and rotated, enabling users to fully explore complete results, in context.
- Can be viewed from an HTML browser on any device, no special software is required.
- Can be easily stored for re-use and future reference. Both the size and number of files is substantially smaller.
- Can be shared with OEMs and suppliers without risk to IP, as the underlying geometry is not shared.
Manufacturers no longer need to settle for manually-produced, low-fidelity simulation result reports
VCollab automates the creation of high-fidelity, actionable simulation results and insights. Analysts spend minutes instead of hours and create far superior simulation insights enabling faster, better design decisions. Design teams, OEMs, and suppliers can collaborate on 3D actionable simulation insights which tell the full story, reducing product costs and timelines.
The Untapped Opportunity in Simulation
Industry analyst Chad Jackson shows how simulation is needlessly constrained, and how VCollab solves these challenges.
Watch the webinar.
Subscribe to our FREE magazine,
FREE email newsletters or both!Latest News
Related Topics
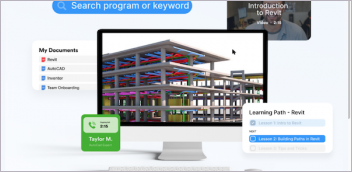
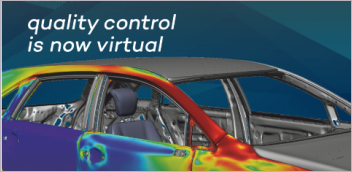
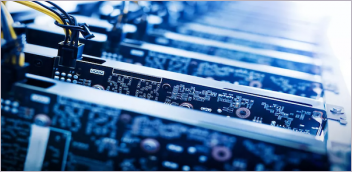
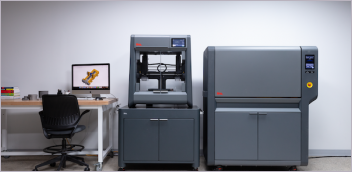