Transforming CAE Reporting, Design Reviews and Decision Time with 3D Digital CAE Information
Leveraging digital 3D data can transform and streamline simulation reporting across the extended enterprise.

Image courtesy of VCollab.
Latest News
January 11, 2023
With highly compressed product development schedules and limited CAE resources, day-to-day operations such as CAE reporting become a challenge with the traditional manual approach. To support confident product design decisions, analysis results must be instantaneously extracted and converted into actionable information, shared among stakeholders to address areas of concern, reviewed collaboratively to determine next steps, and ultimately implemented in the final design. Fortunately, the technology to leverage 3D digital reporting and cut development times and costs is readily available.
From design through manufacturing, today’s new product development processes are driven by robust digital applications. With reduced dependence on physical prototyping, CAE simulations have become critical in making design decisions. All aspects of CAE simulations are driven by 3D applications, with one notable exception: For many manufacturers and product development organizations, CAE analysis reporting for design validation and review remains largely a manual 2D process.
With nearly 80% of a product’s total cost committed at the upstream design stage, today’s accelerated product development processes place a greater emphasis on simulation. Design Engineers, Release Engineers, and other stakeholders rely on feedback from CAE analysis to guide critical product design decisions. This feedback is often in the form of 2D, non-interactive static documents such as PowerPoint slides, images or videos. These formats are decades-old and simply not designed to operate in today’s 3D digital environment, and limit the opportunity for full realization of benefits from CAE simulations.
Within the current static, 2D reporting process, simulation insights need many iterations before they can be shared throughout the extended enterprise or with OEMs and suppliers. The consequences are extensive administrative work by costly CAE Analysts, and a lack of insight to guide critical decision-making.
A Lack of Clarity
These non-interactive 2D document formats, limited in terms of scope and detail, are generally focused on specific views or aspects of the model. This prevents reviewers from gaining insights outside of what was provided in a static report. Consequently, critical decisions are being made based on low-fidelity simulation reports.
Work and Re-Work
Simulation and analysis hold the key to product performance and quality, innovation, and ultimately bottom-line profitability. With a wealth of knowledge and proficiency with complex simulation applications, the contributions of CAE analysis experts are unquestioned. Unfortunately, these experts spend several days or more processing results manually, extracting important CAE insights and preparing CAE reporting documentation in 2D for collaborative design reviews. What’s more, because of the 2D manual reporting limitations, design teams often request additional analysis information creating more rework for the analyst and minimizing their ability to take on other critical simulation needs.
A Transformational Approach
As a CAE analyst for India’s Space Research Organization, Prasad Mandava was all too familiar with the bottlenecks associated with inefficient CAE reporting processes.
“It was clear that while design, analysis, and simulation technologies were making tremendous advancements, the reporting process remained largely stagnant and had not kept pace,” he explained. “For manufacturers the clock is constantly ticking regardless of CAE status. Every minute counts and the window of opportunity for simulation to have an impact is shrinking. We have too much 3D digital information at our fingertips to be sharing this valuable information on PowerPoint slides.”
This revelation led to the formation of Visual Collaboration Technologies, Inc. (VCollab). With VCollab, the 3D CAE simulation results model is the report. Leveraging digital 3D data transforms and streamlines simulation reporting across the extended enterprise and with global OEMs and suppliers. Reducing or eliminating non-value-added manual tasks, bottlenecks, and delays.
Now, analysts can extract, create, update, and share results in minutes. And CAE Managers, Analysts, Designers, Release Engineers, and other stakeholders can collaborate freely and in real-time making comparisons and annotations without going back to the analyst.
VCollab in Action
GKN Automotive is the automotive industry’s only supplier focused on drive system technologies. The company is the world's number one supplier of essential driveline components, all-wheel drive systems, and electric drive systems.
Simulation experts at GKN Automotive in the US and Mexico use VCollab to share simulation results with design engineers and other internal and external customers.
VCollab has allowed GKN to:
- Increase the usefulness of information shared in simulation result reports using 3D animation
- Reduce the potential for error and save analyst time by automatically identifying hotspots in simulation results
- Provide greater design insight into simulation results by showing multiple stress loads in one interactive view
- Improve comparison capabilities by showing multiple design variations one interactive view
- Provide more meaningful end-user reporting with no iterations
- Create HTML browser-viewable simulation results ― simplify access for stakeholders
“VCollab has more than lived up to our expectations for making it faster and easier to create simulation reports. Instead of spending additional time producing slide decks of static 2D results for our customers,” said the company’s Engineering Manager. “VCollab lets us quickly and easily create 3D results which they can pan, zoom, rotate, and animate, to understand the simulation more completely and thoroughly. This has led to better and faster design decision-making.”
Similarly, Amsted Automotive (Saginaw, MI) is achieving measurable benefits in its implementation of VCollab software. The group combines design and engineering expertise, strategically aligned to be a nimble leader in advanced metal-forming and powder metal manufacturing with electro-mechanical clutch design capabilities for electrified propulsion solutions and builds on Amsted Automotive Group’s integral role in global advanced automatic transmissions designed in North America, Europe, and Asia.
Amsted Automotive’s CAE Manager, George Coppens explains that VCollab implementation is having a measurable impact on the time and cost associated with the reporting and sharing of critical simulation results.
“PowerPoint report decks can exceed 100 pages and often take up to five days to create. With VCollab, all the stresses can be displayed in a single viewpoint reducing the process to just a single day in some cases. VCollab’s 3D digital reports allow us to zoom, rotate, and animate to probe multiple areas of the model; and the Hot Spot finder in VCollab quickly uncovers potential areas of concern. Understanding simulation results more completely helps accelerate product development while enhancing product quality and innovation.”
Leveraging Digital Data
Throughout industry, CAE leadership is faced with the challenge to streamline and accelerate product development through engineering analysis efficiency. But traditional simulating reporting methods waste resources and create bottlenecks as CAE analysts can spend up to 30% of their time manually creating reports. At the same time, 2D reports lack the fidelity needed to support informed decision-making.
For a growing number of companies, the answer lies in leveraging digital 3D data to transform simulation post-processing and reporting. This allows CAE managers, analysts, designers, release engineers, and other stakeholders to collaborate more freely and utilize the most accurate and complete information to make key product design decisions. For CAE, now more than ever, interactive, 3D reporting technology needs to take its place alongside the many other 3D technologies that exist in product development.
Subscribe to our FREE magazine,
FREE email newsletters or both!Latest News
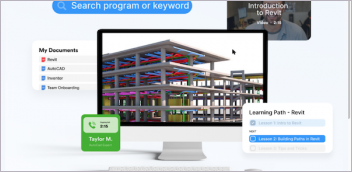
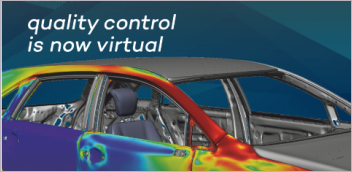
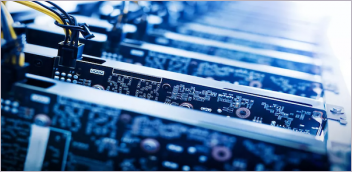
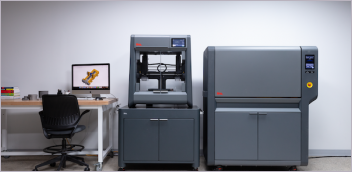