Editor’s Pick: Discrete Element Method Software Updated

Simulations can be conducted from within the easy to use GUI or via a command line interface. Image courtesy of DEM Solutions Ltd.
May 14, 2014
Dear Desktop Engineering Reader:
Designing machinery that handles bulk materials for mining and process manufacturing is more of a job than building CAD assemblies and some physical prototypes. You also analyze and optimize the gear with CFD (computational fluid dynamics), MBD (multibody dynamics) and FEA (finite-element dynamics). But how do you simulate the interaction of the equipment with the material that it is intended to handle? And how do you assess the forces and loading of granular materials whether coal, pills, corn or some powder as they interact with your machine’s components? Today’s Pick of the Week is how.
EDEM from DEM Solutions is high-performance DEM (discrete element method) simulation software that helps you design and optimize equipment for handling and processing bulk materials through understanding how materials behave in your system and how they affect the machinery. The company says that it is the only commercially available software capable of generating DEM simulations and analysis required to solve complex problems in the design, prototyping and optimization of equipment to handle and process bulk solid materials.
EDEM is a DEM platform that works as a complement to your CAE toolkit. The platform is made up of three main components — a preprocessor, a solver and a postprocessor — as well as optional extension modules, including CFD coupling, MBD coupling and an API (applications programming interface).
EDEM’s preprocessing tools include imports of CAD models of equipment and templates of representative model particle shapes and particle-scale physics models along with built-in particle initialization. You can store the specifics of a model’s particle shape and size distribution as well as its mechanical, material and other physical properties in a library and build a collection specific to your needs.
The EDEM solver does the particle-scale physics calculations. It’s based on a sphere-element particle primitive that can generate multi-element particles to represent non-spherical particles. The post-processor comes with a set of data analysis and 3D visualization tools including fast image rendering and video generation as well as data mining and export capabilities.
The newest EDEM release, version 2.6, enables you to export force data from EDEM into ANSYS Mechanical. The export to ANSYS Mechanical automatically structures force data into a text file format that can be imported into ANSYS, which should reduce post-processing operations greatly. Once you import the force data into ANSYS, it can be interpolated to a mesh and complete the analysis. As an side, the company says that work is also underway to extend this functionality to other FEA systems.
DEM Solutions reports that version 2.6 now comes with three wear models that let you see the energy imparted through material contact directly on the equipment surface. These models can display energy imparted both tangentially and normal to the surface, meaning that they can help you identify if an area gets impact strikes or undergoes abrasive wear. It also has a Archard wear model that lets you calibrate a model to give an estimation of wear depth.
Version 2.6 also has a banded particle size distribution tool that helps you work with materials that do not have a standard or uniform size. Essentially, this enables you to analyze materials filtered or sieved through successively smaller mesh sizes.
In total, EDEM version 2.6 has more than 40 enhancements, ranging from official support for Red Hat Linux 6.0 to speedier CAD import and more flexible licensing. You can read more about EDEM version 2.6 in today’s Pick of the Week write-up. But you have to take in some of the videos linked after the main write-up. They are all just a half-minute more or less, but you should really enjoy what they show you. This is really neat stuff.
Thanks, Pal. — Lockwood
Anthony J. Lockwood
Editor at Large, Desktop Engineering
Read today’s pick of the week write-up.
This is sponsored content. Click here to see how it works.
Subscribe to our FREE magazine,
FREE email newsletters or both!About the Author

Anthony J. Lockwood is Digital Engineering’s founding editor. He is now retired. Contact him via de-editors@digitaleng.news.
Follow DE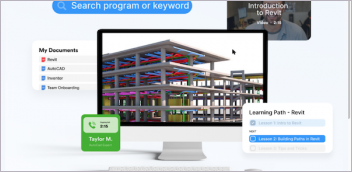
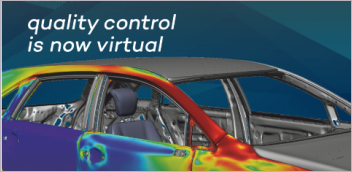
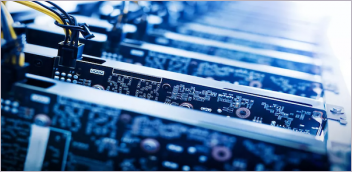
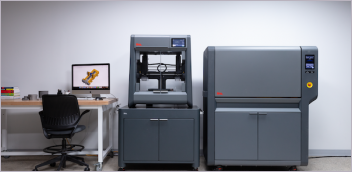