
Image courtesy of Getty Images.
Latest News
December 20, 2024
As we reach the end of 2024, Digital Engineering has asked its design and engineering readers once again to provide insight into their use of design and simulation technology.
The technology landscape for engineers has continued to evolve, with a number of mergers and acquisitions in the simulation and design software space as well as in the 3D printing industry; the emergence of artificial intelligence (AI)-based tools for simulation; increased adoption of graphics processing unit (GPU) acceleration across design, simulation and now computer-aided manufacturing (CAM) vendors; and further adoption of cloud and high-performance computing (HPC) solutions for increasingly complex modeling and simulation tasks.
Last year at this time, AI and machine learning (ML) had just emerged as a viable tool for simulation. Over the past 12 months, major vendors like Siemens, Altair, Autodesk, Ansys, Monolith and others have announced AI-based modeling and simulation tools, as well as AI assistants, and chip industry heavyweight NVIDIA unveiled more AI-based solutions that are relevant for designers.
For this year’s survey, we received responses from more than 200 readers. The largest group of respondents described their primary role as product or system design engineering (32%), followed by engineering management (13%), research & development (12%) and corporate management (9%). Respondents were spread among market sectors, with the majority working in aerospace/aviation/defense, industrial machinery and products, electronic products and equipment, and automotive.
Engineering Challenges
For the second year in a row, respondents listed recruitment and staffing as their biggest challenge, with 84% saying it was extremely or somewhat important (down from 89% last year). Lack of appropriate training for staff and collaboration tied for second at 87%, while short product development deadlines ranked third at 84%. In 2023, the third most common listed challenge was inefficient workflows.
We also asked readers about the importance of sustainability in design. The number of respondents who said sustainability was extremely important dropped from 31% in 2023 to 25% in 2024, while those that thought it was somewhat important rose from 50% to 53%. Respondents who said it was not important at all rose from 19% last year to 22% in the current survey.
We have also seen less focus on sustainability issues among engineering technology vendors, but interestingly, when asked for elaboration from those who did and did not consider sustainability important, we had very few negative comments—in past years, respondents did not hold back when criticizing sustainability initiatives. This year, most of the comments were fairly positive. Here are a few examples:
- I firmly believe that sustainability isn’t just a buzzword anymore, it’s a must-have for companies like ours. The tech industry, especially semiconductors, has a big impact on the planet. From the materials we use to how we make our chips, we can make a real difference. By designing products that are greener, we not only help the Earth but also make our company look good and stay competitive. It’s the right thing to do, and it’s good business, too.
- Environmental sustainability is a fundamental consideration in our design and engineering activities. We prioritize eco-friendly materials, energy-efficient processes, and designs that minimize waste and resource consumption. By integrating sustainability into our practices, we not only meet regulatory requirements but also align with consumer expectations and contribute to a more sustainable future.
- We are a European company (French) and the Europeans are taking environmental stability very seriously as they want to know how your product affects the environment both throughout the lifespan and at the end before they might do business with you.
AI Expands its Footprint
When we asked which technologies readers thought would have the biggest impact on product development in the next five years, AI once again took the top spot at 64% (down slightly from 65% last year). Simulation was second at 43% (up from 38%), followed by HPC/cloud computing (36%—up from 31% last year), additive manufacturing (34%), generative design (31%—up from 29% last year), and advanced materials (28%).
Reader comments on the value and utility of AI in engineering varied from bullish to skeptical:
- AI and machine learning are transformative technologies that can significantly enhance product design and development. They enable more efficient data analysis, automate repetitive tasks, and provide insights that inform better decision-making. By leveraging these technologies, we can create more personalized products, optimize performance, and reduce time to market, ultimately leading to greater customer satisfaction and competitive advantage.
- I envision AI ideally being used for outlier projects, which would normally present higher risk due to unknowns. AI could potentially reduce the uncertainties and increase the human comfort level with what are currently higher risk and navigate such projects in a way that optimizes cost/lead time. Consequently, order intake can be increased along with gross profit and hopefully TNS.
- My organization designs engineering samples of semiconductors. Moreover, I’ve always believed that AI and machine learning are like having a super-smart lab assistant for our semiconductor designs. They can analyze tons of data to find patterns we might miss, helping us optimize everything from circuit layouts to material selection. For instance, AI can predict which materials will perform best under different conditions, saving us time and resources. And machine learning can even help us design new semiconductor architectures that are more efficient and powerful. It’s like having a secret weapon in our development process.
- They will be important but are currently over-hyped. People expect them to be able to do things that they cannot do.
- We have been using the technology for 20 years. It makes impossible tasks possible and will gain an ever more prominent role within our products.
- I am very convinced that AI and machine learning [are] a definite game changer for production in many industries. I feel the impact that they would have on product design will be phenomenal. My only hope is that we focus on regulations and the security aspects as this evolves. Once this is done we will see a faster and much safer evolution.
- AI has potential to benefit engineering; however, I worry that it will be overused, becoming detrimental to critical thinking. Not every tool is an asset.
- Huge AI impact on industrial product design. Machine Learning can make a big difference in manufacturing/ processing.
- Have to be very careful of AI and machine learning. This is something that is only as smart as the people programming it.
Simulation Leads the Way
We again asked readers what technologies they were currently using or developing products for, as well as which technologies they expected to adopt in the next two years. Simulation software once again ranked as the top technology that most readers were currently using, with 56% reporting that they were doing so (up from 50% last year). Additive manufacturing/3D printing was second again at 42%.
Those were followed by product lifecycle management (PLM; 41%), advanced materials and HPC/cloud (tied at 32%), and AI/machine learning (29%—up from 22% last year). HPC/cloud jumped from 22% currently using in 2023 to 32% this year.
In the next two years, 38% of respondents plan to incorporate AI/machine learning in their design/development processes (compared to 35% last year), with predictive analytics, digital twins and generative design tied at around 25% for future deployments. Although virtual/augmented reality current usage was at just 9%, 23% planned to deploy within two years.
Additive Gains Ground in Production Parts
The number of additive manufacturing users that focus primarily on prototyping dropped again this year to 82% from 86% last year (and 89% in 2022). Testing applications were up a lot from 55% last year to 68% this year. End-use part printing rose from 44% of current users to 48%.
Improving product quality jumped to the top of the cost justification list, with 71% saying it was extremely important. Discovering new designs dropped from 72% last year to just 59% this year, tying for second place with shortening product development schedules and reducing product development costs. Other important objectives included fostering innovation, engineering productivity, and reducing manufacturing costs.
When it came to satisfaction with additive manufacturing solution benefits, 54% of users were very satisfied with the technology’s ability to shorten product development schedules, while 45% cited being able to create designs that were not feasible with other technologies. Reducing part complexity was cited by 39% of respondents, followed by reducing development costs (36%).
Respondents also shared their thoughts on the potential of additive manufacturing, along with some examples of how they are currently using the technology.
- Additive manufacturing along with AI is the next big frontier. We don’t use it much yet, but I suspect over time it will become more commonplace with where I work.
- Additive Manufacturing and 3D Printing have the potential to revolutionize product design and development by enabling greater design freedom and rapid prototyping. These technologies allow for the creation of complex geometries that traditional manufacturing methods can’t achieve, leading to more innovative solutions. Additionally, the ability to quickly iterate designs and produce low-volume custom parts can significantly reduce lead times and costs, making it easier to adapt to market demands.
- Awesome, limited by imagination and budget. Still not as accepted as it should be, at least amongst my colleagues.
- The technology continues to improve year to year. 10-15 years ago I would have never imagined using an FDM print as a production part but there are viable options now. I think many companies that have not leveraged additive have no idea what they are missing out on. Investing in this technology seems to spawn continuous improvements and fresh ideas leading to reduced lead times, better costs, less waste and sometimes even marketability with the right audience.
- I think it provides a window into verification of actual part performance, and can provide insights into part behavior that [aren’t] always predicted with full accuracy in simulation.
- Still concerned about using it for load carrying members. Not sure if material homogeneity and mechanical properties for complex alloys can be assured.
Generative Design, Digital Twins Still Treading Water
Generative design adoption is still slow, with just 16% of respondents reporting they are using the technology (up slightly from 14% last year). Moving forward, 26% plan to deploy it in the next two years, again up from 22% last year. When listing objectives for generative design deployments, respondents cited shortening development schedules (61%), manufacturing design that would otherwise not be feasible (43%), and reducing development costs (42%).
Current users said they were most satisfied with generative design’s ability to help them discover new designs (47% were extremely satisfied), followed by fostering innovation (50%) and reducing weight (41%).
Although generative design solutions are being somewhat overshadowed by AI systems, they are much more mature. Respondents had mixed thoughts about the technology:
- As it’s based on simulation theory, it can offer design directions, but still falls short of real-world testing.
- Generative design software is a game-changer in product design, allowing for the exploration of numerous design alternatives based on defined parameters and constraints. Its ability to generate innovative solutions that may not have been considered manually can significantly enhance creativity and efficiency in our development process. This technology not only accelerates the design phase but also optimizes performance and sustainability, ultimately leading to higher-quality products.
- High cost of entry. Need high level of engineering supervision and knowledge of environmental conditions to use successfully. In the appropriate case it is viable for part cost time, safety. The impact will be less than properly trained and thinking engineers assessing the same problem.
- So far not really impressed. Cool geometry is just that. It still has to be manufactured, and GD will lack in that area or limit to certain processes that may not be optimal for part performance and cost. We can’t give up on Design for manufacturing, and Design for manufacturing and assembly.
- Limited utility in well-defined, highly-constrained problem areas. Best at optimization for existing products, but needs hand holding and guidance to succeed.
Digital twins are likewise being adopted very slowly, with 58% of respondents reporting that they do actually know what a digital twin is (up from 54% last year). Just 17% of respondents report they are currently using digital twins (up from 14%); 25% reported they plan to deploy digital twins within the next two years (up from 18%). Asked if they were currently using or planning to implement a PLM/product data management or digital thread solution, 40% said yes.
Simulation Revolution Continues
The majority of respondents agree that simulation-led design will be the most likely technology to revolutionize design engineering processes, with 58% answering in the affirmative (up from 54%). AI was second at 55%, followed by additive manufacturing (49%) and HPC/cloud and generative design, which roughly tied at 40% and 39%, respectively.
Asked about familiarity with various technologies, simulation again led with 83% of respondents being very or somewhat familiar, followed by additive manufacturing (78%), PLM (77%), and HPC/cloud computing (69%). DE
Subscribe to our FREE magazine,
FREE email newsletters or both!Latest News
About the Author

Brian Albright is the editorial director of Digital Engineering. Contact him at de-editors@digitaleng.news.
Follow DE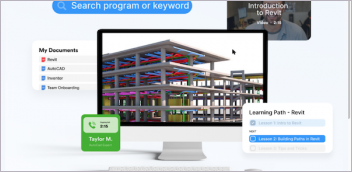
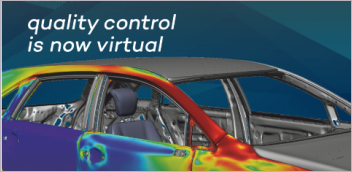
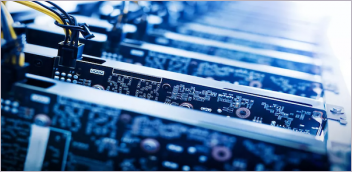
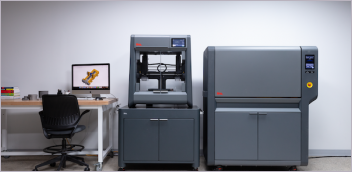