Hexagon Launches Mould and Die Suite
Aim is to empower teams to simplify the work of complex manufacturing.

Hexagon’s Mould and Die Suite. Image courtesy of Hexagon.
Latest News
September 26, 2023
Hexagon’s Manufacturing Intelligence division has released HxGN Mould & Die, a suite of dedicated CAD/CAM (computer-aided design and manufacturing), engineering and automation tools empowering mould and die and tool manufacturers to increase efficiency and produce quality tools for their customers across industries ranging from automotive to aerospace, the company says.
The suite was developed to empower mould designers and makers to exceed operational capabilities in the design and manufacturing of plastic injection moulds, progressive dies, forming dies and similar tools.
Capabilities of the suite include CAD/CAE (computer-aided design and engineering) for plastic injection mould design, CAD/CAE for progressive die design, CAD for manufacturing preparation, CAM for CNC (computer numerical code) machine-tool programming, process simulation and G-code verification and optimization, shop-floor production intelligence, and automation and collaboration powered by Nexus, Hexagon’s digital-reality platform. The suite’s simulation tools help manufacturers understand the feasibility of mould-making processes with actionable information.
“We took everything we know about mould-and-die manufacturing, including our best-in-class Hexagon technologies, to build a specialised suite that empowers mould and die shops of any size to get the best results faster,” says Chuck Mathews, general manager, production software at Hexagon. “Their competitive edge will be enhanced by Nexus, which connects desktop software via the cloud to provide further automation and collaboration opportunities. It also gives teams an easy way to share 3D models with customers through secure web-based visualization, and consolidate access to libraries for tooling, fixtures and materials from their desktop apps.”
“The HxGN Mould and Die suite is an exciting development, combining our customers’ challenges with our deep domain knowledge to achieve more. We are refocussing innovation to bring our ecosystem technologies together and help production teams make better informed decisions, faster,” adds Parth Joshi, chief product and technology officer at Hexagon.
For plastic-injection mould manufacturers, the suite provides tools for design and engineering, flow simulation, reverse engineering, automated electrode design and CNC machining. It builds upon Hexagon’s VISI and WORKNC software, providing multi-axis CAM programming capabilities, direct modeling of solids and surfaces, and supports the construction, editing and repair of complex 3D geometry. Reverse engineering tools allow mould makers to efficiently create solid models from scanned data.
The suite also provides plastic flow analysis tools that help shop-floor teams produce moulds that will perform as required. These simulation capabilities are simple to use. The creation of intricate or difficult-to-machine injection mould features is simplified with the automated design and simulation of EDM (electrical discharge machining) electrodes and their associated holders.
For progressive die manufacturers, HxGN Mould and Die offers a connected workflow with tools for design and engineering, simulation and production. It enables the step-by-step unfolding of surface and solid models, which gives designers more control over the development of each forming stage. Flexible strip layout capabilities and the ability to simulate the performance of the strip at any stage in the design process make it easy to quickly analyze the results of design changes. The software also helps manufacturers predict springback and offers compensation strategies when challenges with material performance are identified.
The suite supports shops in utilizing advanced machine tools, using Hexagon VISI and WORKNC software to help programmers optimize machining cycles and specialized cutting strategies specific to mould production. Prior to machining, CNC programs can be simulated and verified using NCSIMUL, the suite’s G-code simulation software, which incorporates the machining environment to generate a digital twin of the machinery, part and processes.
Sources: Press materials received from the company and additional information gleaned from the company’s website.
More Hexagon Coverage
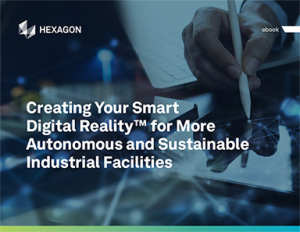
Subscribe to our FREE magazine,
FREE email newsletters or both!Latest News
About the Author

DE’s editors contribute news and new product announcements to Digital Engineering.
Press releases may be sent to them via DE-Editors@digitaleng.news.
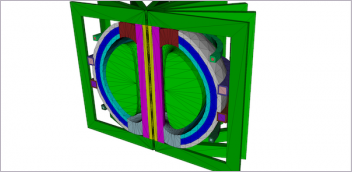
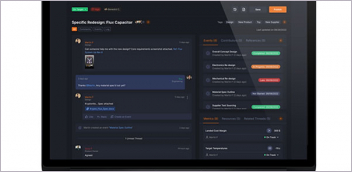
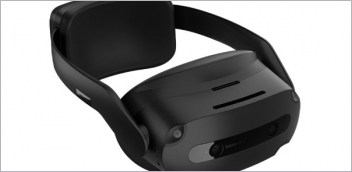
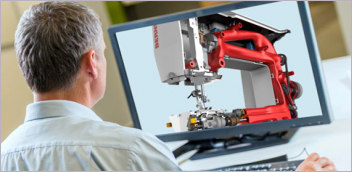